Home> | Automation | >Picking & sortation | >Pick that one out |
ARTICLE
Pick that one out
12 December 2012
Picking boosted for Coop Danmark A/S in new high-bay warehouse SSI Schaefer completed the installation of a new high-bay warehouse (HBW) including tailored WMS for Denmark's leading consumer goods retailer, Coop Danma
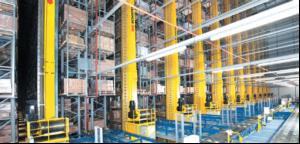
Picking boosted for Coop Danmark A/S
in new high-bay warehouse
SSI Schaefer completed the installation of a new high-bay warehouse (HBW) including tailored WMS for Denmark's leading consumer goods retailer, Coop Danmark A/S.
The three-block HBW, which now serves as a supply and transfer warehouse, has four aisles per block with over 36,000 storage locations for single-deep storage of pallets that can weigh up to 1000 kilograms each. Twelve storage and retrieval machines, that move at a speed of up to 250 metres per minute, ensure quick storage and retrieval of more than 500 pallets per hour.
Running alongside the HBW is the WMS that controls the manual low-bay warehouse, storing positions for manto- goods order picking of fast-moving items, available across three shelf levels.
Items delivered on pallets are logged in goods receiving and transferred to the HBW or block storage. Articles, which for example will have CDs added, are allocated to workstations immediately and then stored in the high bay warehouse as a new stock item. Smaller, high-value items are stored in a separate paternoster system.
Order picking shelves with an attached gravity-roller-conveyor were installed for small volume commodities that are not large enough to be picked directly from the pallet. Systems were supplied from the HBW or the manual warehouse - depending on the advertising campaign.
Up to 25,000 order lines for just under 600 orders are processed daily - five partially linked order picking strategies are designated for this task. Each HBW block is equipped with a picking station to palletise items for large orders.
Controlled by the WMS, source pallets are retrieved from the HBW and allocated for order picking at six source positions in each block. There, supported by height adjustable, ergonomically designed working platforms, items are picked from the source pallets onto seven target pallets.
Partially used and pre-picked pallets are stored in the HBW again; empty pallets are removed automatically. Readily picked target pallets are transferred to consolidation points. If commissioned work is complete and automatic load secured, they are forwarded directly to the three dispatch areas via the conveyor and lift systems. In addition, the WMS arranges for the disposal of packaging waste which is collected in lattice boxes and removed by forklifts.
Due to the high portion of smaller consignments (approx. 30%) that have to be picked in order commissioning, Coop followed the recommendation of SSI Schaefer and created a separate picking area for this range of articles. A three-level flow rack with a total of 120 channels for up to five bins each was installed and connected to the pick positions for larger consignments. The facility is also equipped with a Pick-by-Light-System.
SSI Schaefer completed the installation of a new high-bay warehouse (HBW) including tailored WMS for Denmark's leading consumer goods retailer, Coop Danmark A/S.
The three-block HBW, which now serves as a supply and transfer warehouse, has four aisles per block with over 36,000 storage locations for single-deep storage of pallets that can weigh up to 1000 kilograms each. Twelve storage and retrieval machines, that move at a speed of up to 250 metres per minute, ensure quick storage and retrieval of more than 500 pallets per hour.
Running alongside the HBW is the WMS that controls the manual low-bay warehouse, storing positions for manto- goods order picking of fast-moving items, available across three shelf levels.
Items delivered on pallets are logged in goods receiving and transferred to the HBW or block storage. Articles, which for example will have CDs added, are allocated to workstations immediately and then stored in the high bay warehouse as a new stock item. Smaller, high-value items are stored in a separate paternoster system.
Order picking shelves with an attached gravity-roller-conveyor were installed for small volume commodities that are not large enough to be picked directly from the pallet. Systems were supplied from the HBW or the manual warehouse - depending on the advertising campaign.
Up to 25,000 order lines for just under 600 orders are processed daily - five partially linked order picking strategies are designated for this task. Each HBW block is equipped with a picking station to palletise items for large orders.
Controlled by the WMS, source pallets are retrieved from the HBW and allocated for order picking at six source positions in each block. There, supported by height adjustable, ergonomically designed working platforms, items are picked from the source pallets onto seven target pallets.
Partially used and pre-picked pallets are stored in the HBW again; empty pallets are removed automatically. Readily picked target pallets are transferred to consolidation points. If commissioned work is complete and automatic load secured, they are forwarded directly to the three dispatch areas via the conveyor and lift systems. In addition, the WMS arranges for the disposal of packaging waste which is collected in lattice boxes and removed by forklifts.
Due to the high portion of smaller consignments (approx. 30%) that have to be picked in order commissioning, Coop followed the recommendation of SSI Schaefer and created a separate picking area for this range of articles. A three-level flow rack with a total of 120 channels for up to five bins each was installed and connected to the pick positions for larger consignments. The facility is also equipped with a Pick-by-Light-System.
MORE FROM THIS COMPANY
- Flexibility is top priority for food and drink client
- Pharma firm increases storage capacity
- Aquabox backed by SSI Schaefer
- The 'All-in-One' compact storage and picking solution
- Small parts picking gets a lift
- Pharma wholesaler invests in plastic totes
- Fast and flexible storage & retrieval
- Accurate order picking
- Automated high bay solution
- Huge automated DC being built in Leeds
RELATED ARTICLES
OTHER ARTICLES IN THIS SECTION