Home> | Lift trucks | >Fleet management | >Web-based fleet management system |
ARTICLE
Web-based fleet management system
12 December 2012
Jungheinrich has launched an online forklift truck fleet management system. Called ISM Online, the system manages, analyses and optimises truck fleets regardless of their size and complexity, giving the user greater fl
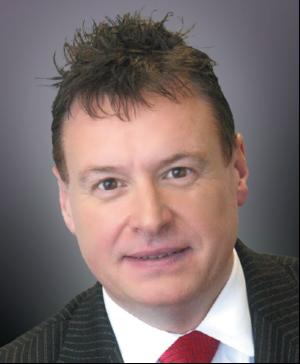
Jungheinrich has launched an
online forklift truck fleet
management system. Called ISM
Online, the system manages,
analyses and optimises truck fleets
regardless of their size and
complexity, giving the user greater
fleet management transparency. If
required to do so, the system works
across several facilities - even if the
sites are in different countries.
ISM Online consists of four different modules. Each module is designed to meet different user requirements and can be operated as a stand-alone system or in combination.
The basis module provides the user with a site-overlapping overview of all master data for the fleet. Apart from the number and age of the trucks at each location, this module also shows the total costs of the fleet at the touch of a button.
The operating costs module also allows a detailed list of costs to be obtained but with this module, the user has the added benefit of receiving information about invoices, operating hours and service reports.
The safety and productivity modules make it possible to document truck damage and address the causes of the damage thanks to access control, driver administration and impact recording functions.
Bill Goodwin, Jungheinrich UK's sales director, says: "The safety and productivity modules will increase the drivers' sense of responsibility.
Apart from delivering significantly more safety in the warehouse, we believe the system will also drive down the costs caused by the improper use of trucks." ISM Online can be used to monitor Jungheinrich trucks as well as other forklift brands.
Truck optimisation Also new from Jungheinrich is a forklift truck route optimisation module for its warehouse management system (WMS).
In simple terms, the system directs the most appropriate truck to the place in the warehouse or distribution centre where it is needed - thereby eliminating 'empty' forklift runs within the store.
"This innovation not only adds efficiency to a logistics system but reduces the costs of operating a forklift fleet," says Steve Richmond (pictured), general manager of Jungheinrich UK's Systems & Projects Division.
Using a predefined set of principles and rules, the Truck Route Optimisation System gathers and processes a wide range of information from the WMS before directing the most appropriate truck in the fleet to where it is needed.
"This ensures that the right truck is always selected for the pending transport job," adds Richmond.
Orders are issued once a variety of optimisation criteria have been processed. Urgent orders are given precedence because the system automatically assigns a higher priority to orders which have not been completed within a certain time frame while the system also takes account of the individual truck specifications to ensure that the right truck is assigned to the right application.
By continuously monitoring the utilisation of the truck fleet, the system further improves efficiency by allowing bottlenecks to be quickly and easily identified and suitable countermeasures implemented.
"Where the new Jungheinrich truck route optimisation module is used there have been quantifiable improvements in the productivity of the equipment and the overall performance of the operation," says Richmond.
ISM Online consists of four different modules. Each module is designed to meet different user requirements and can be operated as a stand-alone system or in combination.
The basis module provides the user with a site-overlapping overview of all master data for the fleet. Apart from the number and age of the trucks at each location, this module also shows the total costs of the fleet at the touch of a button.
The operating costs module also allows a detailed list of costs to be obtained but with this module, the user has the added benefit of receiving information about invoices, operating hours and service reports.
The safety and productivity modules make it possible to document truck damage and address the causes of the damage thanks to access control, driver administration and impact recording functions.
Bill Goodwin, Jungheinrich UK's sales director, says: "The safety and productivity modules will increase the drivers' sense of responsibility.
Apart from delivering significantly more safety in the warehouse, we believe the system will also drive down the costs caused by the improper use of trucks." ISM Online can be used to monitor Jungheinrich trucks as well as other forklift brands.
Truck optimisation Also new from Jungheinrich is a forklift truck route optimisation module for its warehouse management system (WMS).
In simple terms, the system directs the most appropriate truck to the place in the warehouse or distribution centre where it is needed - thereby eliminating 'empty' forklift runs within the store.
"This innovation not only adds efficiency to a logistics system but reduces the costs of operating a forklift fleet," says Steve Richmond (pictured), general manager of Jungheinrich UK's Systems & Projects Division.
Using a predefined set of principles and rules, the Truck Route Optimisation System gathers and processes a wide range of information from the WMS before directing the most appropriate truck in the fleet to where it is needed.
"This ensures that the right truck is always selected for the pending transport job," adds Richmond.
Orders are issued once a variety of optimisation criteria have been processed. Urgent orders are given precedence because the system automatically assigns a higher priority to orders which have not been completed within a certain time frame while the system also takes account of the individual truck specifications to ensure that the right truck is assigned to the right application.
By continuously monitoring the utilisation of the truck fleet, the system further improves efficiency by allowing bottlenecks to be quickly and easily identified and suitable countermeasures implemented.
"Where the new Jungheinrich truck route optimisation module is used there have been quantifiable improvements in the productivity of the equipment and the overall performance of the operation," says Richmond.
MORE FROM THIS COMPANY
- Flexible MHE contract for 3PL
- Jungheinrich hire fleet for Halloween
- Emissions cut
- A tow tractor for tight spots
- Reach trucks 'ready to go'
- Jungheinrich makes strategic investment in robotic specialist
- Jungheinrich makes four senior appointments to Systems division
- Compact pallet truck
- Jungheinrich Safety pavilion aims to prevent accidents
- Parts centre
OTHER ARTICLES IN THIS SECTION