Home> | Automation | >Conveying components | >Fashion for flatpacked |
ARTICLE
Fashion for flatpacked
12 December 2012
Dutch fashion retailer and wholesaler Veldhoven installed an automated system from SDI Group in its new DC as it shifted the emphasis of its goods-in operation from hanging garments to flatpacked products from its product
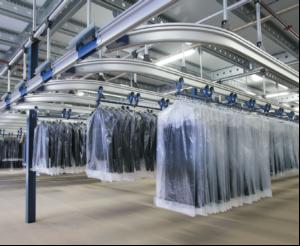
Dutch fashion retailer and wholesaler Veldhoven
installed an automated system from SDI Group in its
new DC as it shifted the emphasis of its goods-in
operation from hanging garments to flatpacked
products from its production facility in China.Simon
Duddy reports from the plant in the Netherlands.
Asignificant trend in fashion retailing is a move to the import of flatpacked rather than hanging garments. The rationale is simple. Increased use of flatpacked goods drives greater efficiencies in transportation. A container can typically carry 8,000 hanging garments as opposed to 32,000 items when flatpacked.
This was an important consideration when Veldhoven, a Dutch fashion retailer and wholesaler, recently opened a new distribution centre in Alphen aan den Rijn in the Netherlands. As a growing organisation it had made increasing logistical efficiencies a priority and appointed consultant Jean-Paul MP Verhaaren to manage the project.
Jean-Paul explains: "The first task was to look at Veldhoven's logistics, and there were various issues. The organisation was growing, facilities were old and processes had to be tightened." Jean-Paul and Veldhoven quickly realised that a new scalable facility with efficient, proven automated technology was the way to go. The company leased a large site where a factory had burned down and built it from the ashes, so to speak, within 16 months.
The facility is 5,051 sq m with an additional 3,990 sq m through mezzanines and has capacity to store 2,200 pallets and 220,000 hanging items.
Jean-Paul researched the project, all the while picturing the needs of this family company some 20 years into the future.
The company was not disposed to take undue risks and only considered proven technology. Jean-Paul adds: "We wanted an integration partner that could handle flat and hanging product. Quality was more important than price and SDI had very good references." A key element of the warehouse design was accommodating both flatpacked and hanging garments in goods in and out, but geared up to dealing with large volumes of flatpacked items. The SDI automated system allowed this.
John Hamilton, sales director, SDI Group explains: "On the flat side, a strong benefit of our automated system is it will allow you to do batch sortation. You can go to a picking slot, and instead of picking individually now you can pick in batches, sorted as independent orders. This improves output and stockholding accuracy.
"It is a complete closed loop, there is no more paperwork for pickers and they don't have to revisit the slots if the products are not there. There is no reworking papers or completing Excel reports. The sorter it does it all within an automated loop and feeds into the WMS." In addition, Veldhoven installed a steam tunnel, which is used to make flatpacked garments presentable for hanging and delivery to shops.
Winnie Ahrens, senior sales manager, SDI Group explains: "You will not find many companies today willing to go through the whole logistics process including tunnel finishing, bagging, and all the value added services.Most companies outsource to specialised third parties, but then they are dependent on others." Previously Veldhoven would also make more deliveries to customers, one truck with hanging garments, one with flatpacked. Due to the new DC and new processes, these operations are combined into a one stop operation.
Traditionally, Veldhoven's various wholesale and retail arms levied a fixed percentage charge for internal services provided by Veldhoven Distribution. This led to difficulties during the recession, with the logistics operation taking a hit as some end user customers had cashflow problems or went bust.
As a consequence, the logistics arm has taken the opportunity to change its model to produce a commercial menu for internal parties, so they pay a set price for every service provided, for example, per product handled and shipped.
The most significant consequence of these developments, in terms of new facilities and equipment and of important process changes, is that they are projected to save the company up to 33% of its logistics budget.
This can be broken down into three key parts. First, Veldhoven is able to transport more products per container from its factory in China by flatpacking. Secondly, the automated nature of the installation means the warehouse can run with 10 full time employees and 10 seasonal employees as opposed to the 40/50 seasonal employees previously needed.
The warehouse revamp also has improved the efficiency of the IT systems with a sophisticated WMS replacing an Excel-based process, improving stockholding accuracy.
In addition, the increased efficiencies mean production capacity exceeds current need, providing scope for growth and also the opportunity to outsource value added services. For example, Veldhoven can offer a steam tunnel service to third parties creating an extra revenue stream.
Environmental impact The new distribution centre also represents a significant improvement in environmental performance for Veldhoven. For one, the move from transporting hanging garments to transporting flatpacked products from production to distribution means fewer containers are used, with fewer trucks needed for transportation.
On the outbound side, previously Veldhoven Distribution used multiple transport companies because the processing of hanging products was outsourced. In the new logistics concept, the processing of both packed and hanging products will take place at the new DC, enabling the company to use one combined transport. This will mean one truck stopping at a shop instead of two.
Here too, this will mean less energy consumed and a considerable reduction in emissions.
The conveyors used in the warehouse only move when there are goods on the belt, meaning more carbon savings. In addition, the materials handling fleet has been switched from gas and diesel forklifts to electrical stackers and man-up trucks.
Order forms for picking orders have been replaced with paper-free, voice-topick systems, with which employees can pick orders by voice. Packing slips will be reduced to the last box in a delivery or sent digitally.
In terms of lighting, the warehouse uses movement detectors that activate the lights only if someone is in the area. The lighting itself uses long-life, highfrequency fittings or energy efficient LED lighting.
CEO Martijn Veldhoven concludes: "Delivering collections to our clients at the right time is only part of the distribution process.We also wanted to provide extra services such as stock management, partial deliveries, and supply of additional client information.
"That's why we are so proud to have developed a future-focused international distribution centre and to have completed the project so quickly."
Asignificant trend in fashion retailing is a move to the import of flatpacked rather than hanging garments. The rationale is simple. Increased use of flatpacked goods drives greater efficiencies in transportation. A container can typically carry 8,000 hanging garments as opposed to 32,000 items when flatpacked.
This was an important consideration when Veldhoven, a Dutch fashion retailer and wholesaler, recently opened a new distribution centre in Alphen aan den Rijn in the Netherlands. As a growing organisation it had made increasing logistical efficiencies a priority and appointed consultant Jean-Paul MP Verhaaren to manage the project.
Jean-Paul explains: "The first task was to look at Veldhoven's logistics, and there were various issues. The organisation was growing, facilities were old and processes had to be tightened." Jean-Paul and Veldhoven quickly realised that a new scalable facility with efficient, proven automated technology was the way to go. The company leased a large site where a factory had burned down and built it from the ashes, so to speak, within 16 months.
The facility is 5,051 sq m with an additional 3,990 sq m through mezzanines and has capacity to store 2,200 pallets and 220,000 hanging items.
Jean-Paul researched the project, all the while picturing the needs of this family company some 20 years into the future.
The company was not disposed to take undue risks and only considered proven technology. Jean-Paul adds: "We wanted an integration partner that could handle flat and hanging product. Quality was more important than price and SDI had very good references." A key element of the warehouse design was accommodating both flatpacked and hanging garments in goods in and out, but geared up to dealing with large volumes of flatpacked items. The SDI automated system allowed this.
John Hamilton, sales director, SDI Group explains: "On the flat side, a strong benefit of our automated system is it will allow you to do batch sortation. You can go to a picking slot, and instead of picking individually now you can pick in batches, sorted as independent orders. This improves output and stockholding accuracy.
"It is a complete closed loop, there is no more paperwork for pickers and they don't have to revisit the slots if the products are not there. There is no reworking papers or completing Excel reports. The sorter it does it all within an automated loop and feeds into the WMS." In addition, Veldhoven installed a steam tunnel, which is used to make flatpacked garments presentable for hanging and delivery to shops.
Winnie Ahrens, senior sales manager, SDI Group explains: "You will not find many companies today willing to go through the whole logistics process including tunnel finishing, bagging, and all the value added services.Most companies outsource to specialised third parties, but then they are dependent on others." Previously Veldhoven would also make more deliveries to customers, one truck with hanging garments, one with flatpacked. Due to the new DC and new processes, these operations are combined into a one stop operation.
Traditionally, Veldhoven's various wholesale and retail arms levied a fixed percentage charge for internal services provided by Veldhoven Distribution. This led to difficulties during the recession, with the logistics operation taking a hit as some end user customers had cashflow problems or went bust.
As a consequence, the logistics arm has taken the opportunity to change its model to produce a commercial menu for internal parties, so they pay a set price for every service provided, for example, per product handled and shipped.
The most significant consequence of these developments, in terms of new facilities and equipment and of important process changes, is that they are projected to save the company up to 33% of its logistics budget.
This can be broken down into three key parts. First, Veldhoven is able to transport more products per container from its factory in China by flatpacking. Secondly, the automated nature of the installation means the warehouse can run with 10 full time employees and 10 seasonal employees as opposed to the 40/50 seasonal employees previously needed.
The warehouse revamp also has improved the efficiency of the IT systems with a sophisticated WMS replacing an Excel-based process, improving stockholding accuracy.
In addition, the increased efficiencies mean production capacity exceeds current need, providing scope for growth and also the opportunity to outsource value added services. For example, Veldhoven can offer a steam tunnel service to third parties creating an extra revenue stream.
Environmental impact The new distribution centre also represents a significant improvement in environmental performance for Veldhoven. For one, the move from transporting hanging garments to transporting flatpacked products from production to distribution means fewer containers are used, with fewer trucks needed for transportation.
On the outbound side, previously Veldhoven Distribution used multiple transport companies because the processing of hanging products was outsourced. In the new logistics concept, the processing of both packed and hanging products will take place at the new DC, enabling the company to use one combined transport. This will mean one truck stopping at a shop instead of two.
Here too, this will mean less energy consumed and a considerable reduction in emissions.
The conveyors used in the warehouse only move when there are goods on the belt, meaning more carbon savings. In addition, the materials handling fleet has been switched from gas and diesel forklifts to electrical stackers and man-up trucks.
Order forms for picking orders have been replaced with paper-free, voice-topick systems, with which employees can pick orders by voice. Packing slips will be reduced to the last box in a delivery or sent digitally.
In terms of lighting, the warehouse uses movement detectors that activate the lights only if someone is in the area. The lighting itself uses long-life, highfrequency fittings or energy efficient LED lighting.
CEO Martijn Veldhoven concludes: "Delivering collections to our clients at the right time is only part of the distribution process.We also wanted to provide extra services such as stock management, partial deliveries, and supply of additional client information.
"That's why we are so proud to have developed a future-focused international distribution centre and to have completed the project so quickly."
MORE FROM THIS COMPANY
- SDI reshuffles management team
- Sortation system handles flat and hanging goods together
- New facilities boost SDI Group's expansion
- No Limit goes live
- SDI Group wins contract to maintain DCs for George at Asda
- SDI group celebrates worldwide success
- SDI Group launches tilt-tray sorter
- Protect your profits
- George at Asda further automates e-fulfilment
- SDI Group launches a sortation knowledge portal
OTHER ARTICLES IN THIS SECTION