Home> | Automation | >Picking & sortation | >Interroll cross belt sorters - the economical solution |
ARTICLE
Interroll cross belt sorters - the economical solution
12 December 2012
Every day, millions of goods are in transit worldwide and this has put enormous demands on internal processing/ scheduling and calls for highperformance logistics with efficient sortation systems. Interroll sorters ar
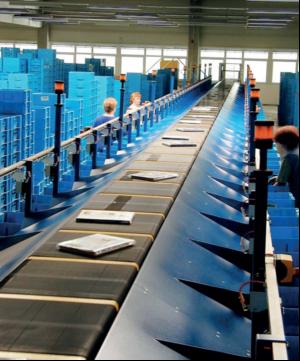
Every day, millions of goods are in
transit worldwide and this has put
enormous demands on internal
processing/ scheduling and calls for highperformance
logistics with efficient
sortation systems.
Interroll sorters are designed to be versatile and capable of handling a wide range of unit loads up to 35kg of all different shapes, sizes and materials (mixed goods) and are ideally suitable for handling awkward or sensitive goods. Systems are extremely reliable, offer high availability and are economical, even for low throughputs of 2,000 items per hour. The design concept enables systems to be easily adaptable to future growth and can provide a quick ROI (Return on Investment), of 2-3 years.
Depending on the application and the available space, you can choose between a horizontal, multidirectional sorter (loop configuration), or a vertical, circulating sorter (linear configuration).
Versatility and accuracy in product handling Interroll sorters quickly and reliably distribute a wide variety of unit loads of all shapes and sizes, weighing anything from 50g to 35kg, small or large, robust or fragile.
Goods are inducted onto the sorter either via direct manual placement, semi automatic merging or by a fully automated infeed system. A wide range of carrier size options facilitates selection of the optimum, carrier for the goods to be sorted and their orientation.
The key elements of these sorters are the cross belt carriers with their patented mechanical discharge principle. The carriers run on quiet, low rolling resistance polyurethane-encased rollers, pre assembled, to precisely manufactured modular sections.
All carriers are connected together to form a 'train' and furthermore each carrier is connected directly to a reinforced rubber drive chain, providing a positive drive to the 'train of carriers' via a single high efficiency motor/gearbox. Once a cross belt carrier reaches its intended destination, a pneumatically actuated paddle makes contact with a drive wheel mounted underneath each carrier transferring drive to the cross belt, which in turn safely sorts the goods to their destination.
Compared to sorters with linear motors, the single high efficiency motor/gearbox utilized in the Interroll sorter translates to even greater cost savings via reduced energy consumption. In addition, the direct drive principle, and a fixed connection between carrier and drive chain, ensures secure tracking of products, For further details via a single, standard industrial encoder.
Interroll sorters are designed to be versatile and capable of handling a wide range of unit loads up to 35kg of all different shapes, sizes and materials (mixed goods) and are ideally suitable for handling awkward or sensitive goods. Systems are extremely reliable, offer high availability and are economical, even for low throughputs of 2,000 items per hour. The design concept enables systems to be easily adaptable to future growth and can provide a quick ROI (Return on Investment), of 2-3 years.
Depending on the application and the available space, you can choose between a horizontal, multidirectional sorter (loop configuration), or a vertical, circulating sorter (linear configuration).
Versatility and accuracy in product handling Interroll sorters quickly and reliably distribute a wide variety of unit loads of all shapes and sizes, weighing anything from 50g to 35kg, small or large, robust or fragile.
Goods are inducted onto the sorter either via direct manual placement, semi automatic merging or by a fully automated infeed system. A wide range of carrier size options facilitates selection of the optimum, carrier for the goods to be sorted and their orientation.
The key elements of these sorters are the cross belt carriers with their patented mechanical discharge principle. The carriers run on quiet, low rolling resistance polyurethane-encased rollers, pre assembled, to precisely manufactured modular sections.
All carriers are connected together to form a 'train' and furthermore each carrier is connected directly to a reinforced rubber drive chain, providing a positive drive to the 'train of carriers' via a single high efficiency motor/gearbox. Once a cross belt carrier reaches its intended destination, a pneumatically actuated paddle makes contact with a drive wheel mounted underneath each carrier transferring drive to the cross belt, which in turn safely sorts the goods to their destination.
Compared to sorters with linear motors, the single high efficiency motor/gearbox utilized in the Interroll sorter translates to even greater cost savings via reduced energy consumption. In addition, the direct drive principle, and a fixed connection between carrier and drive chain, ensures secure tracking of products, For further details via a single, standard industrial encoder.
MORE FROM THIS COMPANY
- Interroll to show off range of solutions at IMHX
- Interroll Automation GmbH appoints MD
- High-performance crossbelt sorter
- Interroll’s second plant in Atlanta starts operation
- Intelligent conveying system improves performance and reduces energy consumption
- Vertical conveying
- New global sales lead at Interroll
- Maximum flexibility with optimised new Carton Wheel Flow
- Centre of Excellence established
- Interroll presents dynamic storage
RELATED ARTICLES
OTHER ARTICLES IN THIS SECTION