Home> | Industry Sector | >Manufacturing | >Smart upgrade |
Home> | Facilities Management | >Recycling | >Smart upgrade |
Smart upgrade
19 November 2019
In May of 2019 Compact & Bale was contacted by manufacturer Westley Plastics to discuss options for replacement balers.
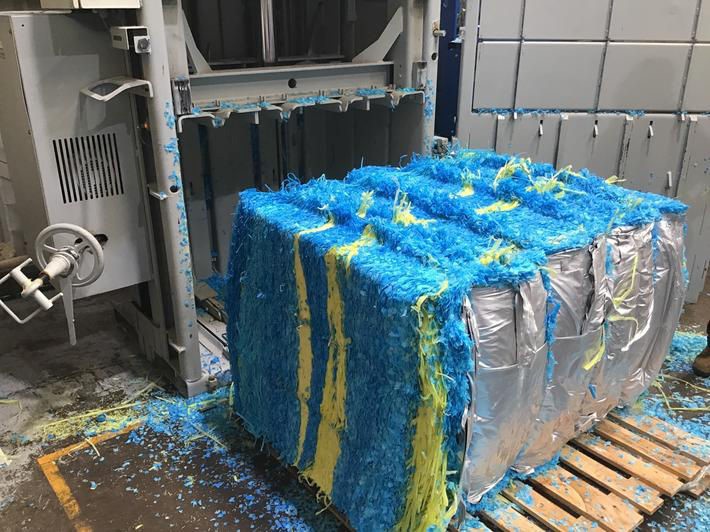
The current models in place at the time were not creating a solid bale which would fall apart on ejection. This led to material having to be re-baled on site, or by its collection partner.
This issue impacts payloads on the collection vehicle as bales can not be stacked properly and with the lower bale weights, both lead to reduced tonnage and a lower rebate paid for the material.
Other third party ‘baler specialists’ had suggested that site upgrade to a horizontal baler, stating that they wouldn’t be able to achieve a solid bale in a vertical baler due to the material.
This was incorrect and typically, a horizontal baler will cost 3-4 x that of a standard mill size vertical baler. Based on the initial questions asked and photos supplied of the material, C&B were able to identify remotely the challenges faced by this customer and immediately outline a solution. The recommendation given and final solution installed was a 54-tonne press force used baler, that was refurbished at a Compact & Bale workshop.
As part of our hire fleet offering of used balers, Westley Plastics is open to upgrading the machine or switching out for a different model as the business grows. Equally should its waste production change, the customer will always have a supportive partner ready to assist with an extensive fleet of machines.