Home> | Lift trucks | >Specialist trucks | >Packing in the pallets |
ARTICLE
Packing in the pallets
12 December 2012
Articulated trucks can help warehouse managers make better use of space offering lower costs per pallet stored, argues Simon Brown md at Translift Bendi Heating, lighting and maintenance all play their part in the i
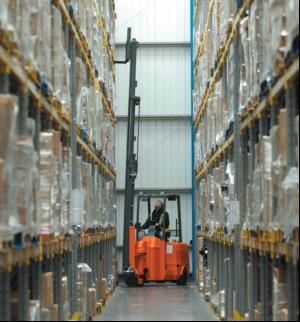
Articulated trucks can help warehouse
managers make better use of space
offering lower costs per pallet stored,
argues Simon Brown md at Translift
Bendi
Heating, lighting and maintenance all play their part in the increasing costs of operating a warehouse, as well as the costs of the property and staffing. Under increasing pressure to trim these costs and achieve reduced carbon emissions, warehouse operators are recognising that the spacesaving abilities of Bendi articulated trucks are creating opportunities for very significant energy savings compared with premises in which counterbalance,VNA or reach trucks operate.
As a rule, warehouses designed for counterbalance or reach trucks in conjunction with APR (adjustable pallet racking) are the least space efficient, with typical aisle widths from 2.8m to 4m+ in common use. However, the aisle width is only part of the equation. Turning and loading/unloading space at the ends of the aisles also accounts for lost space.Many VNA (very narrow aisle) machines achieve the same aisle widths as Bendis but require on average 30% of the warehouse to be dedicated to transfer aisles, marshalling areas and P&D stations (to hold stock going to and from the VNA racking). This wasted space costs money to build, heat, light, maintain and pay rent and business rates on.
Imagine a 100m x 120m warehouse, 10m high block stacked to the roof with 100,000 off 1m tall blue Chep pallets stacked floor to ceiling, back to front. If the rates, rent, lights, staff and equipment costs etc, come to £x per month, then the cost per pallet stored is x/100,000 per month. This storage method is utopian and rarely suits real life warehousing in terms of stock rotation, accessibility or the ability of products to support themselves while stacked this way.More often than not, product has to be 100% accessible. This is why APR is so prevalent.
Using APR and a standard counterbalance, the building will only store 10,496 pallets (assuming a 4m aisle and counterbalances being limited to about 6m of lift, so the product can only be stacked 4 high allowing for clearances). In this example, the warehouse is only utilising a miniscule 10% of its total cubic space, leaving 90% as very costly fresh air. The storage cost per pallet is £x/10,496, of which energy for light and heat makes a significant percentage in most premises.
A reach truck, working in a 2.85m aisle but allowing a 15m marshalling/drop area for the counterbalance, because the reach is unsuitable to go outside, will store 20,720 pallets, if stored 7 high. This is almost twice the storage capacity of a standard counterbalance, cutting the storage cost per pallet by almost half - and this is why they are so popular throughout the world.
The next step up in efficiency is brought by wire guided VNAs working in 1850mm aisles, with a 7m end of aisle transfer (the space required to move from aisle to aisle). This solution requires an additional 15m marshalling/drop area for the pallet trucks or counterbalance trucks to take pallets to and from the system, so storing 7 high will squeeze in 24,500 racked pallets. This equates to 3780 more pallets or 18% more than the warehouse with reach trucks, with the corresponding improvements in building energy utilisation.
In the 1960s this was the state-of-the art warehouse solution.
However, the need for flat floors, guidance systems, slow throughputs and additional equipment adds cost and complexity.
These were the factors which inspired Freddy Brown, the pioneer of man-up VNA, to develop a better and more cost-effective solution: the Bendi.
A Bendi truck working in 1696mm aisles (1600mm is the minimum aisle width - building permitting) will also store 7 high but only requires a transfer aisle of 2.6m, which unlike VNAs can be bridged. This configuration achieves 30,680 pallets stored. That's almost 50% more than the reach truck and 25% more than the VNA - therefore offering significantly lower costs and a much smaller carbon footprint per pallet stored. In fact the Bendi offers the same storage capacity as a warehouse operating counterbalance truck in just 33% of the space. That makes the warehouse using Bendi trucks 66% more energy efficient.
As described previously, lost storage space at the end of aisles can be greatly reduced when operating articulated trucks. This is not only because the trucks are more manoeuvrable, but also because there's no requirement for other types of vehicle within the warehouse, to load and unload alongside the warehouse trucks. Bendi articulated trucks can stack and de-stack pallets and load or unload them to or from lorries in your yard, saving space and time - and further reducing carbon emissions.
The outstanding stability and improved point loading characteristics of Bendi articulated trucks allows their immediate use in all warehouses, including those with standard floor finishes and speculatively built flatness grades as commonly in use with counterbalance trucks - even where racking up to 12m high is used. This eliminates the requirement for costly specialist flooring or grinding of existing floors. There is also no requirement for guidance rails or wires as is usually the case with VNA systems.
Bendi articulated trucks are able to operate in external yards - even where the ground is uneven or broken. Additionally we have produced a guidebook, covering all aspects of articulated truck theory and practice called The Warehouse Revolution.
Heating, lighting and maintenance all play their part in the increasing costs of operating a warehouse, as well as the costs of the property and staffing. Under increasing pressure to trim these costs and achieve reduced carbon emissions, warehouse operators are recognising that the spacesaving abilities of Bendi articulated trucks are creating opportunities for very significant energy savings compared with premises in which counterbalance,VNA or reach trucks operate.
As a rule, warehouses designed for counterbalance or reach trucks in conjunction with APR (adjustable pallet racking) are the least space efficient, with typical aisle widths from 2.8m to 4m+ in common use. However, the aisle width is only part of the equation. Turning and loading/unloading space at the ends of the aisles also accounts for lost space.Many VNA (very narrow aisle) machines achieve the same aisle widths as Bendis but require on average 30% of the warehouse to be dedicated to transfer aisles, marshalling areas and P&D stations (to hold stock going to and from the VNA racking). This wasted space costs money to build, heat, light, maintain and pay rent and business rates on.
Imagine a 100m x 120m warehouse, 10m high block stacked to the roof with 100,000 off 1m tall blue Chep pallets stacked floor to ceiling, back to front. If the rates, rent, lights, staff and equipment costs etc, come to £x per month, then the cost per pallet stored is x/100,000 per month. This storage method is utopian and rarely suits real life warehousing in terms of stock rotation, accessibility or the ability of products to support themselves while stacked this way.More often than not, product has to be 100% accessible. This is why APR is so prevalent.
Using APR and a standard counterbalance, the building will only store 10,496 pallets (assuming a 4m aisle and counterbalances being limited to about 6m of lift, so the product can only be stacked 4 high allowing for clearances). In this example, the warehouse is only utilising a miniscule 10% of its total cubic space, leaving 90% as very costly fresh air. The storage cost per pallet is £x/10,496, of which energy for light and heat makes a significant percentage in most premises.
A reach truck, working in a 2.85m aisle but allowing a 15m marshalling/drop area for the counterbalance, because the reach is unsuitable to go outside, will store 20,720 pallets, if stored 7 high. This is almost twice the storage capacity of a standard counterbalance, cutting the storage cost per pallet by almost half - and this is why they are so popular throughout the world.
The next step up in efficiency is brought by wire guided VNAs working in 1850mm aisles, with a 7m end of aisle transfer (the space required to move from aisle to aisle). This solution requires an additional 15m marshalling/drop area for the pallet trucks or counterbalance trucks to take pallets to and from the system, so storing 7 high will squeeze in 24,500 racked pallets. This equates to 3780 more pallets or 18% more than the warehouse with reach trucks, with the corresponding improvements in building energy utilisation.
In the 1960s this was the state-of-the art warehouse solution.
However, the need for flat floors, guidance systems, slow throughputs and additional equipment adds cost and complexity.
These were the factors which inspired Freddy Brown, the pioneer of man-up VNA, to develop a better and more cost-effective solution: the Bendi.
A Bendi truck working in 1696mm aisles (1600mm is the minimum aisle width - building permitting) will also store 7 high but only requires a transfer aisle of 2.6m, which unlike VNAs can be bridged. This configuration achieves 30,680 pallets stored. That's almost 50% more than the reach truck and 25% more than the VNA - therefore offering significantly lower costs and a much smaller carbon footprint per pallet stored. In fact the Bendi offers the same storage capacity as a warehouse operating counterbalance truck in just 33% of the space. That makes the warehouse using Bendi trucks 66% more energy efficient.
As described previously, lost storage space at the end of aisles can be greatly reduced when operating articulated trucks. This is not only because the trucks are more manoeuvrable, but also because there's no requirement for other types of vehicle within the warehouse, to load and unload alongside the warehouse trucks. Bendi articulated trucks can stack and de-stack pallets and load or unload them to or from lorries in your yard, saving space and time - and further reducing carbon emissions.
The outstanding stability and improved point loading characteristics of Bendi articulated trucks allows their immediate use in all warehouses, including those with standard floor finishes and speculatively built flatness grades as commonly in use with counterbalance trucks - even where racking up to 12m high is used. This eliminates the requirement for costly specialist flooring or grinding of existing floors. There is also no requirement for guidance rails or wires as is usually the case with VNA systems.
Bendi articulated trucks are able to operate in external yards - even where the ground is uneven or broken. Additionally we have produced a guidebook, covering all aspects of articulated truck theory and practice called The Warehouse Revolution.
MORE FROM THIS COMPANY
- Anything else is a Waste of Space
- Bendi promotes three to director level
- Translift Bendi and HUBTEX join forces in the UK
- Bendi saves space, time & money
- Double pallets handled
- Bendi Order Picker up for FLTA Award
- Bendi is Innovation winner
- Bendi sales hit the 9000 mark
- Innovation trumps slumps
- Trucks facilitate growth
OTHER ARTICLES IN THIS SECTION